The lattice ball mill is mainly composed of six parts: cylinder, feeder, discharger, transmission device, bearing and lubrication system. The ground material in the lattice ball mill is discharged along with the pulp through the discharge holes on the partition. The pulp surface at the discharge end is lower than the pulp outflow surface of the intermediate shaft neck, which is a low-level, forced discharge. The grid type ball mill can load more balls due to the existence of the grid plate, and it is convenient to load small balls. The productivity of the grid type ball mill is about 20%-30% higher than that of the overflow type ball mill. Although the power consumption is higher than that of the overflow type of the same specification, it is lower than the power consumption.
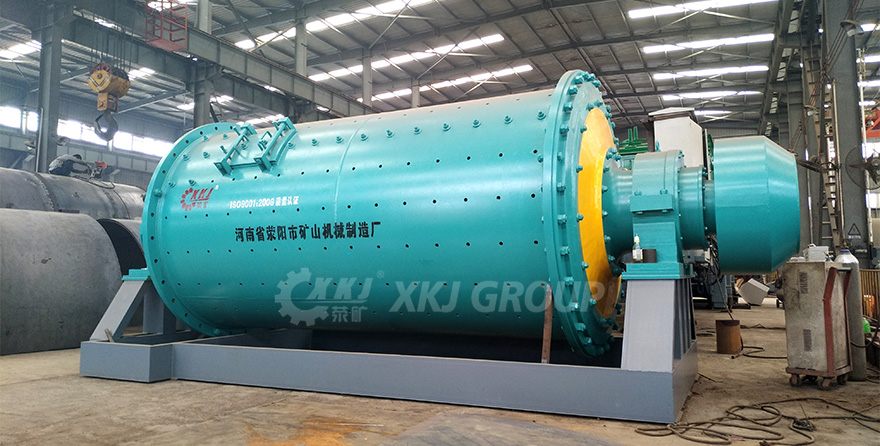
Compared with the lattice type ball mill, the overflow type mill does not have a fan-shaped lattice plate device in the discharge part, and the diameter of the hollow shaft at the discharge end is larger than the feed end, thus forming a certain height difference between the mine end and the slurry surface at the discharge end. Prompt the ground pulp to be retained at the discharge end and be removed through the discharge port, so it is called an overflow ball mill. Due to the large processing capacity of the grid-type ball mill and the less over-crushing of the product, there is a current trend of preferential use of the grid-type ball mill. Because the ground product of the overflow type ball mill is overflowed and removed from the journal in the discharge, the grinding time is long and the product particle size is fine, so the ground product particle size is -0.1mm or -0.074mm. Score>80%. Generally, in the grinding process at both ends, the lattice type ball mill is mostly used in the first stage, and the overflow type is mostly used in the second stage of fine grinding.